Permanent Wood Foundations
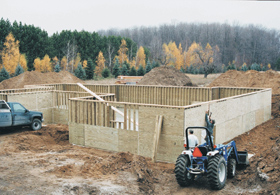
- Wood foundations are simpler, quicker and cheaper to construct than masonry foundations. On average, they will not, however, last as long as masonry foundations and are less durable in the long-term.
- The design of PWFs requires that dry soil is maintained around the foundation. This means that a properly maintained and constructed basement with wood walls will be dry and mildew-free. Basement mildew, leakage and dampness are common in houses with masonry foundations.
- Finishing a basement is easier when walls are made from wood. Insulation is placed between the wall studs to which drywall can be attached.
- The basement will be warmer because wood is a better insulator than masonry, and the foundation wall studs provide large cavities for insulation. However, it must be considered that wood foundation walls are typically much thinner than masonry walls. Also, masonry can be insulated.
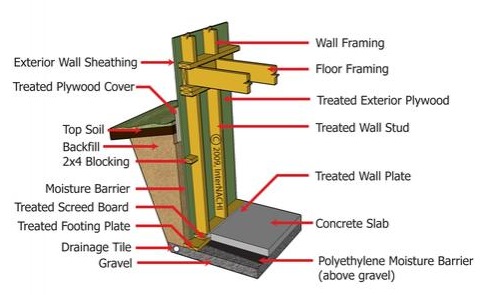
- dampness. If dampness is present, its source should be identified. Dampness may be due to a rising water table, an inadequate drainage system, or inadequate damp-proofing. Water from an interior source, such as an air conditioner or a high-efficiency furnace, however, does not indicate a compromised PWF.
- exterior wood decay. Inspectors can check for exterior wood decay by probing the wall from the outside with a rod. It is usually adequate to probe once every 8 feet. If decayed wood is detected by probing, it is likely that decay exists elsewhere in the wall.
- interior wood decay. If the interior wall is not covered by drywall, it may be possible to inspect for wood decay below grade from the inside of the house.
- foundation leakage. Evidence of foundation leakage may be discovered at butt joints where sealant may not have been used.
- buckling. Buckling can occur due to constant pressure over the course of years, or by the back-filling process.
- lack of a moisture barrier. Outside, a moisture barrier should be present and it should rise above grade.
- bowing of the foundation walls, especially the wall next to the basement stairs.
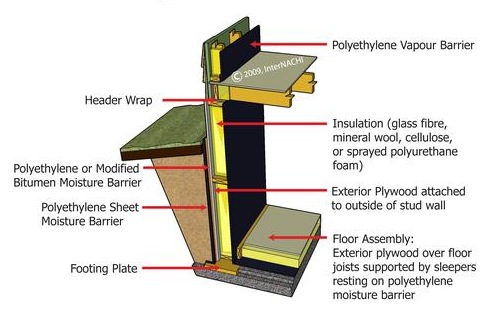
Plywood panel joints in the foundation walls shall be sealed full length with a caulking compound capable of producing a moisture-proof seal under the conditions of temperature and moisture content at which it will be applied and used.
A 6-mil-thick (0.15 mm) polyethylene film shall be applied over the below-grade portion of exterior foundation walls prior to backfilling. Joints in the polyethylene film shall be lapped 6 inches (152 mm) and sealed with adhesive. The top ledge of the polyethylene film shall be bonded to the sheathing to form a seal. Film areas at grade shall be protected from mechanical damage and exposure by a pressure preservatively treated lumber or plywood strip attached to the wall several inches above finish-grade level and extending approximately 9 inches (229 mm) below grade. The joint between the strip and the wall shall be caulked full length prior to fastening the strip to the wall. Other coverings appropriate to the architectural treatment may also be used. The polyethylene film shall extend down to the bottom of the wood footing plate but shall not overlap or extend into the gravel or crushed stone footing.
In summary, permanent wood foundations are relatively new and rare, but InterNACHI inspectors should know the defects that are commonly associated with them.